“By producing hand sanitizer, it is gratifying to know that we are doing something that actually might help another human being from getting infected by the virus.”
— Mason alum Bill Karlson, co-founder and CEO of KO Distilling in Manassas, Virginia
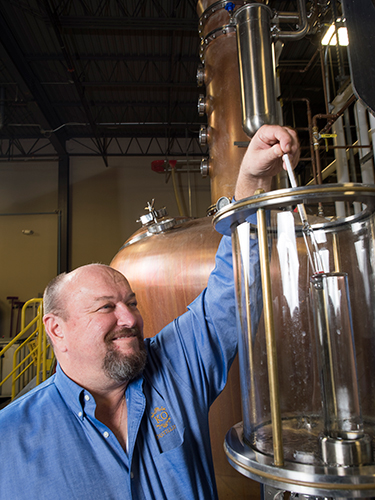
Mason Engineering alum Bill Karlson, co-founder and CEO of KO Distilling, is making Bare Knuckle Hand Sanitizer during the coronavirus crisis. He's pictured here at his craft distillery before the pandemic.
Bill Karlson, MS Software Systems Engineering ’94, is distilling a new solution to fight the coronavirus.
In late March, when he heard that other craft distilleries across the country had begun making much-needed hand sanitizer during the coronavirus pandemic, Karlson and his team decided to join the sanitizing army with their business, KO Distilling in Manassas, Virginia. Its original products are Bare Knuckle whiskeys and Battle Standard 142 gins.
“Hand sanitizer requires 80 percent ethanol, of which we can produce a lot,” says Karlson, the company’s co-founder and CEO. “Last year, we produced about 65,000 proof gallons of distilled spirits using approximately 350 tons of Virginia grains. So, we gladly and quickly made the pivot.”
Karlson initially plans to donate Bare Knuckle Hand Sanitizer to Manassas-area first responders, hospitals, charitable organizations, and nursing homes. Additional quantities are being sold through government channels or to essential businesses to help cover production costs and support the continued employment of the distillery’s 15 employees.
To manufacture hand sanitizer, KO Distilling incorporated some changes in their facility. “Thankfully, we didn’t have to completely retool the distillery,” Karlson says. “What we did have to do is modify our mashing, fermenting, and distilling processes to be able to produce 170 proof ethanol, which we had never done before. That proof is needed because compounding with other sanitizer ingredients dilutes the ethanol down to 160 proof.”
They bought a few thousand pounds of hydrogen peroxide, glycerol, and a denaturant, which makes the alcohol undrinkable. They also needed to stock up on thousands of five-gallon pails, lids, and many other supplies, he says.
Karlson and his team set up a 4,000-square-foot area, which is about the size of a basketball court, in the distillery for employees to safely and efficiently compound, label, fill, seal, palletize, and ship hand-sanitizer pails.
They switched to a 10-hour, seven-day production schedule to make about 1,600 gallons of hand sanitizer a week. “We opted to go with five-gallon pails, each of which has a secured lid with an extractable spout, which will allow for easy and safe pouring and refilling,” he says.
The company is limiting its sales to the Virginia, Washington, D.C., and Maryland-area. “We already have a substantial pipeline of large orders from local customers.”
KO Distilling is still making and selling its other products.
Karlson, who is retired from a career as an executive with a government contracting company, says his education at Mason helped in the business world. “What I learned at Mason was how to apply the knowledge you learn in a classroom to solving real-world problems.”
He’s not sure how long they’ll be making Bare Knuckle Hand Sanitizer. “Like everyone else, we are hoping the pandemic subsides quickly, but we are prepared to make hand sanitizer not only during the remainder of the pandemic but for weeks and even months after the pandemic is over because sanitizer product supply chains will take a while to rebound.”
In the meantime, he’s thankful that he and his team can help. “When you make and sell spirits, you get satisfaction from knowing you are making a quality product that people will like,” Karlson says. “By producing hand sanitizer, it is gratifying to know that we are doing something that actually might help another human being from getting infected by the virus.”